
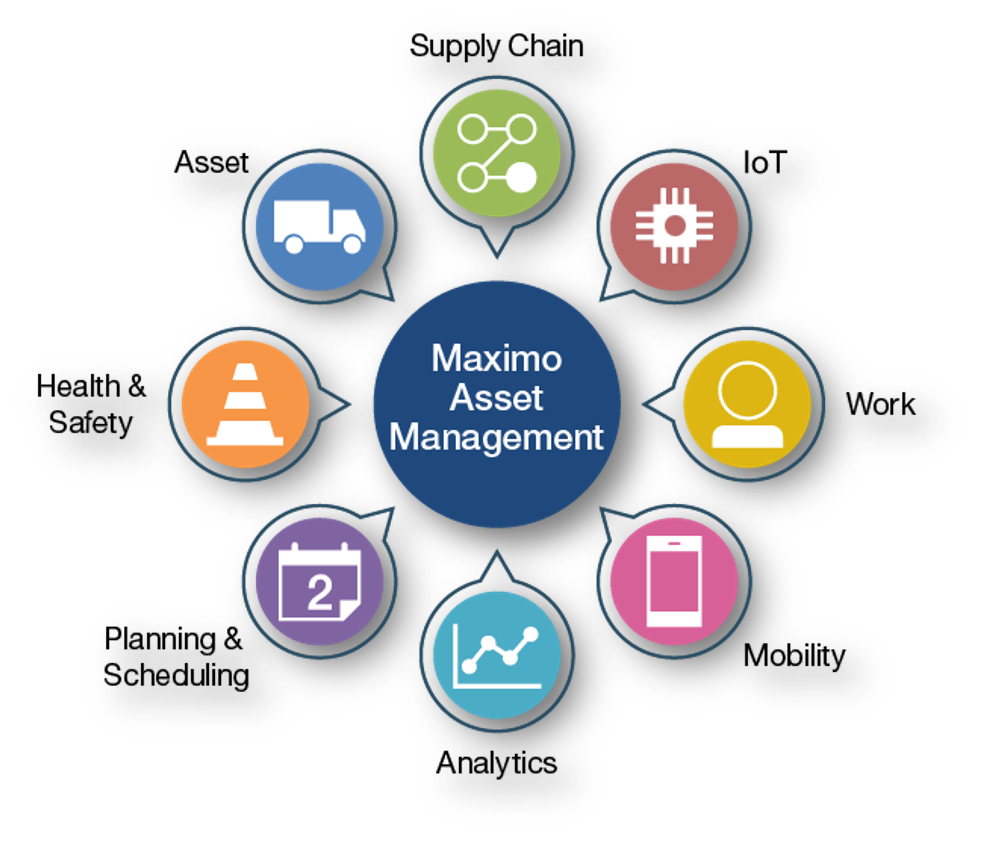
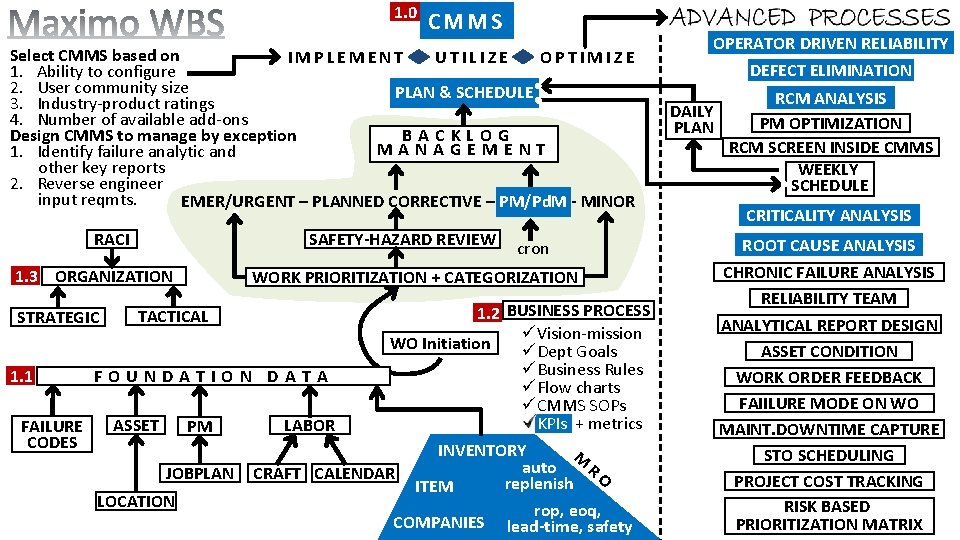
In addition to cost savings, other benefits include improved workplace safety, enhanced productivity and minimized human error.Īll forms of maintenance management share the common objective of analyzing production and finding the best practices and processes within a specific field. Maintenance management helps improve the operational efficiency of plant facilities, which contributes to revenue by decreasing operating costs and improving the quality (and quantity) of manufactured products. Unplanned downtime causes a snowball effect, leading to a spike in unexpected costs associated with things like repairs (overtime labor, spare parts, etc.), delayed shipments, lost revenue or complete breakdowns of machines. Properly maintained assets and resources keep your production stable and greatly minimize the chances for unplanned downtime.
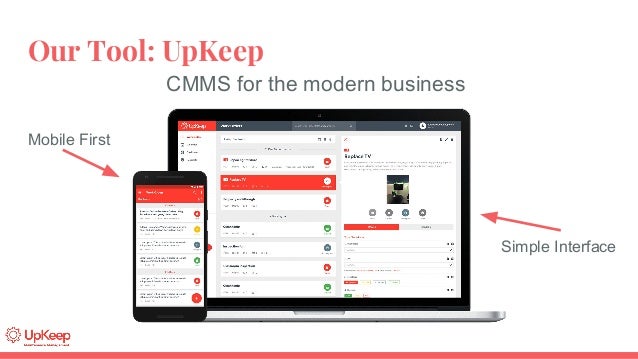
Maintenance management is vital in ensuring the long-term success of your maintenance program by monitoring quality assurance, maintaining operational efficiency and keeping assets in optimum running order. If you need additional support or expertise in the process of shifting your matntenance management practices, bringing in reputable reliability and maintenance experts like those at IDCON could help you idetify opportunities and create an achievable plan for improvement. Improving maintenance management should be a continuous goal for any company with machine assets, but there is no one-size-fits-all solution. Whether you're using a condition-based maintenance program like predictive maintenance or a more time-based maintenance program like preventive maintenance, it's important to focus your program on the type of maintenance used and its role within your organization. Maintenance management programs are highly customizable and centered around the type(s) of maintenance employed at a plant. Maintenance management isn't just a software system - it's a combination of software, best practices and trained personnel, all focused on the same goal. Maintenance management has gone from an archaic, tedious, handwritten process to a computerized maintenance management system (CMMS) - a software that plans, tracks, measures and optimizes all forms of a maintenance program in one central system.
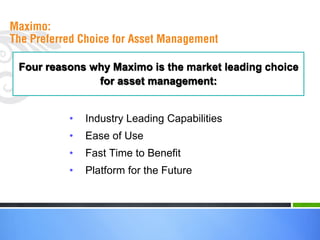
Maintenance management is defined as the process of maintaining a company's assets and resources while controlling time and costs, thereby ensuring maximum efficiency of the manufacturing process. Maintenance Management is the process of maintaining a company's assets and resources while controlling time and costs, ensuring maximum efficiency of the manufacturing process.
